Insulating a roof
I seem to have gone through a pattern of insulating roof space’s the last couple months, not something I’m keen on doing but it was for some of my regulars.
So I thought I would write a little article about insulation especially for a loft/attic space to help you out.
The guidelines haven’t changed much the last few years but a good amount of insulation to have is 270mm thick and this is what the EPC assessors will be looking for if you’re trying to get your rating up to let a property.
“Remember from April 2018 the EPC rating has to be Grade E or higher for any new tenancy agreements.”
But to be honest they do everything in increments of 100mm thick now so you will probably end up with 300mm anyway.
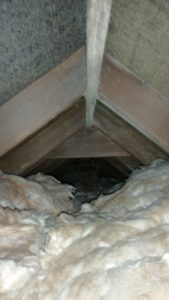
There is no real easy way of doing this job, its horrible stuff to work with. I find doing it in the winter months is best as its cooler in the attic, obviously not a good idea to work in an attic in the summer time as its way to hot especially if you are wearing all the PPE. As minimum with this stuff I wear full overalls, mask, hat and gloves, also a head torch for the dark corners.
Loft insulation is relatively easy stuff to work with a good Sharpe Stanley knife is more than capable enough to cut it. Oddly enough the 200mm thick insulation is easier to cut then the 100mm, I find I always end up tearing the 100mm to get it to separate.`
I have done a lot of shitty old jobs over the years, so I seem to be able to switch off from feeling really uncomfortable and just crack on till the job is done. However for newbies just getting into this world of prolonged hard jobs, I have a few tips.
- Break the job up into small tasks, so get a certain area covered, then have a breath of fresh air, then start again.
- Have targets “I want to get that area and that area done by break time”
- Don’t waste a trip, so if you need to go down and get something like a saw, bring something else that you may need later up with you on your return.
- If you’re on your own I have mentioned this before in my “tips for beginners in construction” post, but I have an audio playing from my phone through the headphones. I love personal development audios and business development so when doing these long hard tasks to help you switch of have a listen to one of these and you will be surprised how much more you can do. The worst thing is to start thinking about how tired you are or how hot it is, the trick is to deter your mind onto other things, the reason I also love the audios is because I feel like I’m learning while earning which is great..
When doing a loft the things you will find hard is the uncomfortable working conditions as I said if your sensible you will have all the overalls and PPE on which in a small roof space is horrible and when you start moving and cutting the insulation you start to get itchy face and arms and that is horrible you will also get really hot just because of the nature of the work and environment, with this type of task I don’t mess around I go up and do the job until its done only stopping for fluids when required I can’t stand taking the mask and hat of every time and having to face putting back on the insulation covered overalls. I also get more covered with the insulation when I’m taking the overalls off so I keep this to a minimum.
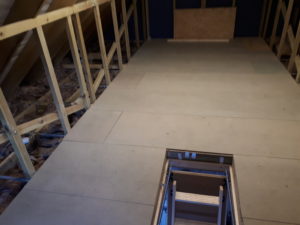
I also find having knee pads on invaluable, roof spaces are usually low so you spend a hell of a lot of time either bent double or on your knees so knee pads are a must and it means you can feel stable while working on the task at hand and not thinking about the pain in your legs. Also an old bricklaying tutor of mine would really get mad with us if he ever saw us working on are knees he would always say if you wanted to last in the job don’t work of your knees and my yoga teacher always says nurse your knees. So basically “look after them”.
There are loads of different types of insulation to work with, the standard fibreglass which we all know well. PIR board which you would probably know as celotex but that’s just the make there are loads like it now. There is also now a space quilt so it has a silver finish that is being used a lot in roof spaces on the rafters. Polystyrene like the stuff they use for packaging and the list goes on some more environmentally friendly versions are sheep’s wool and hemp insulation which are good alternatives, they are more expensive but are sustainable.
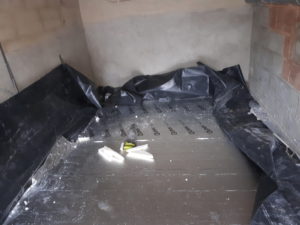
The PIR board is the most used in general building duties nowadays due to the easy handling plus the great thermal ratings its achieves at the relatively small thicknesses. However I have heard on a couple of training sessions I have been on recently that when its used retrospectively, so on older properties in floor or between rafters that they are very inefficient due to the twist and turns of the older timber, so actually it might not be filling in between the wood work as much as we would of liked. I think on newer work it’s a good product but alternatives should be looked at on the older properties.

The Rockwool slab as mentioned on my products page is a good alternative it has a good thermal and acoustic rating and it’s easier to fill the spaces between the woodwork as it can be pushed in places more freely.
I have used both now a lot and to be honest I seem to react badly to the PIR board even wearing all the PPE the fibres just really don’t agree with me and I feel shitty after using the stuff. Whereas the Rockwool type insulation although an irritant on the skin doesn’t make me feel as sniffly as the PIR.
The other product I have heard a lot about recently is one called Hybris. A quote from the spec is as follows:
“It’s a reflective insulation product for timber frame or masonry walls, pitched roofs or ceiling applications. Based on a honeycomb structure made of shaped polyethylene foams glued to aluminium coated polyethylene foils. High thermal performance is provided by a special structure composed of a large number of low emissivity cavities, protected from dust and excessive air movement. Moreover, the low emissivity external films provide additional thermal resistance, when associated with air cavities.”
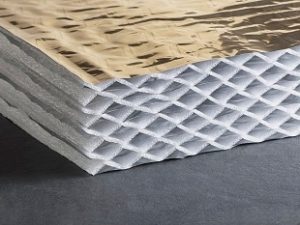
I know a lot of trades that deal with insulation recommend this product, due to the fact there is no dust particles created when cutting the stuff and it is easy install, also its cut slightly larger than required, which will fill in the gaps on twisted timbers, so this is a product to look out for and one that I will try and install on my next project.
Hopefully I have motivated you to get your loft space up to spec and bring your carbon footprint down and also a bit more knowledge on different types of insulation.
Thanks for reading.
Toby.